Draco Systems SL
Production ready for SmartFactory 4.0
Please contact us
Our story
With more than two decades of setting the pace in the technology sector, Draco Systems is proud to announce its natural evolution: the strategic leap into third-party assembly. This decision is not only a reflection of our vast experience, but also our constant commitment to innovation and excellence. Using the most advanced technology in machinery and embracing total digitization, we position ourselves at the forefront of Industry 4.0, setting a new standard in electronic manufacturing.
At Draco Systems, we understand that the heart of exceptional service lies in the ability to anticipate and exceed our customers’ expectations. For this reason, we have invested unreservedly in state-of-the-art technology and comprehensive digitization processes that allow us to offer personalized, flexible and top-quality solutions. From design and development to production and final assembly, every step is optimized through intelligent and automated systems, ensuring unprecedented efficiency and precision.
Our approach to Industry 4.0 not only improves our production capacity, but also strengthens traceability and transparency throughout the entire manufacturing process. This commitment to innovation and quality does not allow us to offer our customers what they really value: reliable, durable electronic engineering solutions and the technological forefront.
By choosing Draco Systems, our customers benefit from a partnership that understands and anticipates their needs, transforming challenges into opportunities and goals into realities. We are proud to be key partners in their success, providing not only exceptional products, but also unmatched added value in the market.
Draco Systems: More than a supplier, we are your strategic partner into the future of electronic engineering innovation. Welcome to the new era of manufacturing, where experience is one with technology to create the extraordinary.
prototypes
Small productions
Pre-series
Great Productions
Purchase management
of components
Management of alternatives
redesign
traceability
Tracking
Smart Factory (5.0)
P&P (SMD)
P&P (Pick and Place) machines represent the cutting edge of surface assembly technology, offering comprehensive and high-precision solutions for the electronics industry. These advanced systems are able to handle a wide range of components with unmatched accuracy, guaranteeing efficient and high-quality production. The flexibility of Siplace machines allows them to be adapted to different production sizes, from small series to large volumes, always ensuring maximum performance. This level of adaptability makes them ideal for a wide variety of applications, from prototyping to mass manufacturing. The precision and reliability of Siplace machines significantly improves production line efficiency, reducing downtime and operating costs, making it a worthwhile investment for any company focused on innovation and quality .
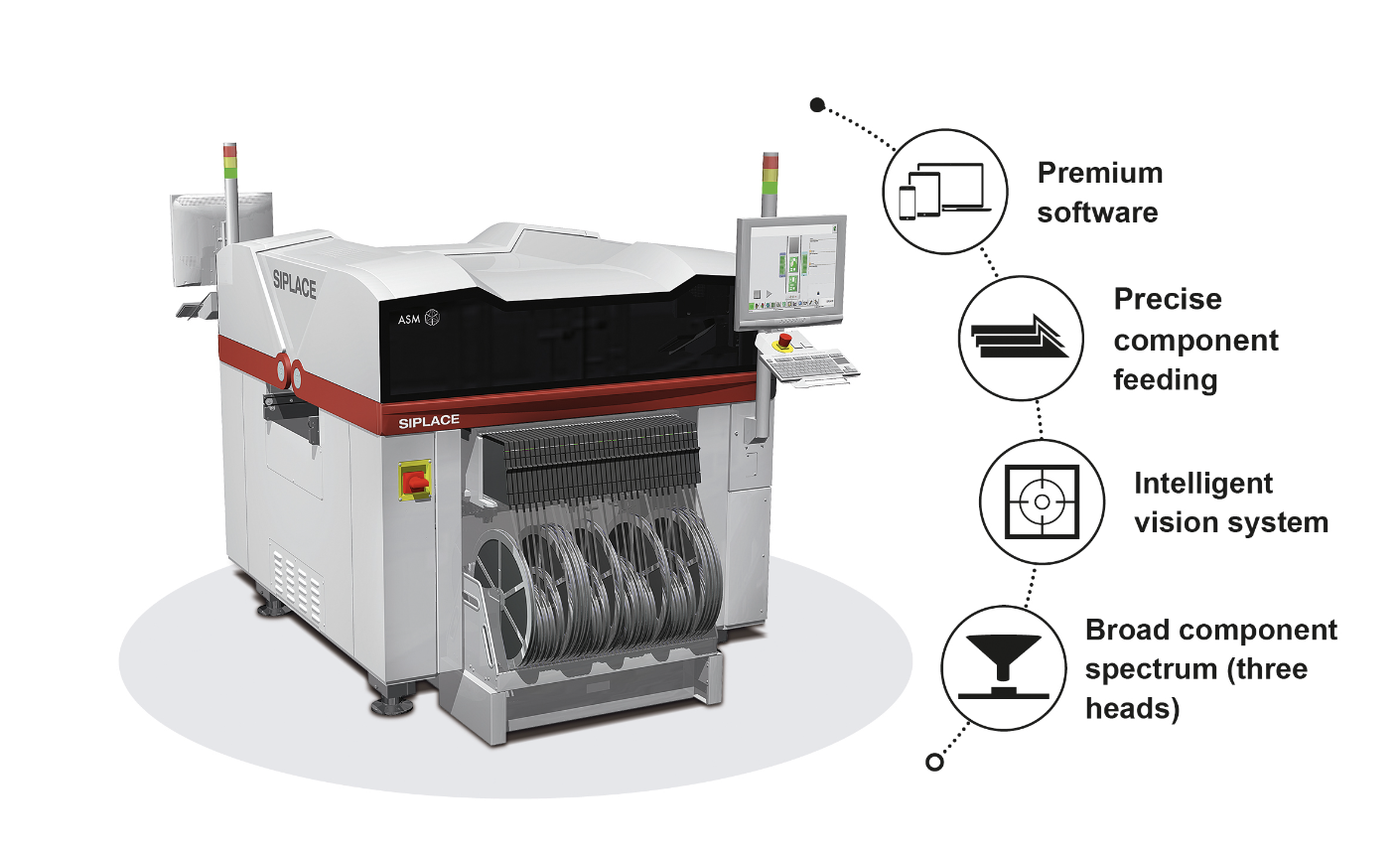
Characteristics:
- High Precision and Reliability : They guarantee the exact placement of components, which is crucial for the integrity and operation of electronic products.
- Versatility in Components : Ability to assemble a wide range of components of different sizes and shapes.
- Adaptability to Various Production Volumes : From small runs to large volumes, allowing scalability without compromising quality.
- Optimization of Production Time : Significant reduction of downtime thanks to its efficiency and speed in assembly.
- Easy Integration with Existing Systems : Compatibility with other production lines and software systems, facilitating a cohesive workflow.
- Intuitive and Advanced Software : Facilitates programming, management and optimization of production, continuously improving processes.
- Commitments to Sustainability : Designed with energy efficiency and reduced environmental impact in mind.
These features make P&P Siplace machines stand out as market leaders, offering companies a powerful tool to improve their production capabilities and stay at the forefront of the electronics industry.
Selective (THT)
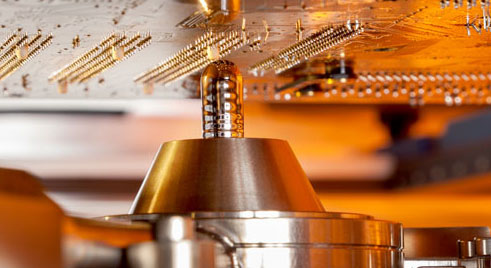
Selective wave soldering, like that of ERSA equipment, represents a significant advance in electronic manufacturing processes, combining efficiency and precision in the application of solder at specific points in circuits. The technology allows companies to achieve superior solder quality on through-hole surface-mounted components, without compromising adjacent components or PCB integrity. The ability to adapt to different batch sizes and the ease of programming of these machines makes them an ideal solution for a wide range of welding applications, from prototypes to mass production, thus ensuring a profitable and lasting investment for any committed company. with excellence in electronic manufacturing.
Traceability – Industry 4.0/5.0
Draco Systems has committed to the implementation of Industry 4.0/5.0 and has radically transformed manufacturing processes, integrating advanced digital technologies to create intelligent and automated production systems. The industrial revolution allows unprecedented traceability from the origin of the components to quality control and final assembly, ensuring complete visibility of the product’s life cycle. The traceability of components and equipment facilitated by Industry 4.0/5.0 guarantees maximum quality and efficiency, allowing companies to respond quickly to market demands, optimize resources and reduce waste. By leveraging real-time data and advanced analytics, companies can predict maintenance, avoid downtime and customize production to previously unimaginable levels, ushering in a new era in manufacturing.
Virtues of Industry 4.0/5.0 and Traceability:
- Complete Visibility : Full traceability from the acquisition of components to final delivery, ensuring quality and compliance with standards.
- Efficiency and Improvement : Optimization of processes through the use of real-time data, to significantly reduce cycle times and increase productivity.
- Flexibility in Production : Ability to quickly adapt to changes in market demand or customize products according to the specific needs of customers.
- Cost and Waste Reduction : Improvement in inventory management and waste reduction thanks to more precise planning and optimized manufacturing processes.
- Predictive Maintenance : Use of sensors and AI to determine errors in equipment before they happen , minimizing downtime and extending the useful life of the machinery.
- Security and compliance : Improvements in security thanks to the automation of dangerous tasks and the ability to track and ensure compliance with international regulations.
- Data-Based Decisions : Ability to make informed strategic decisions based on the analysis of complex data, improving competitiveness and innovation.
- Customization at Scale : Mass custom production that allows you to offer unique products to each customer without compromising efficiency.
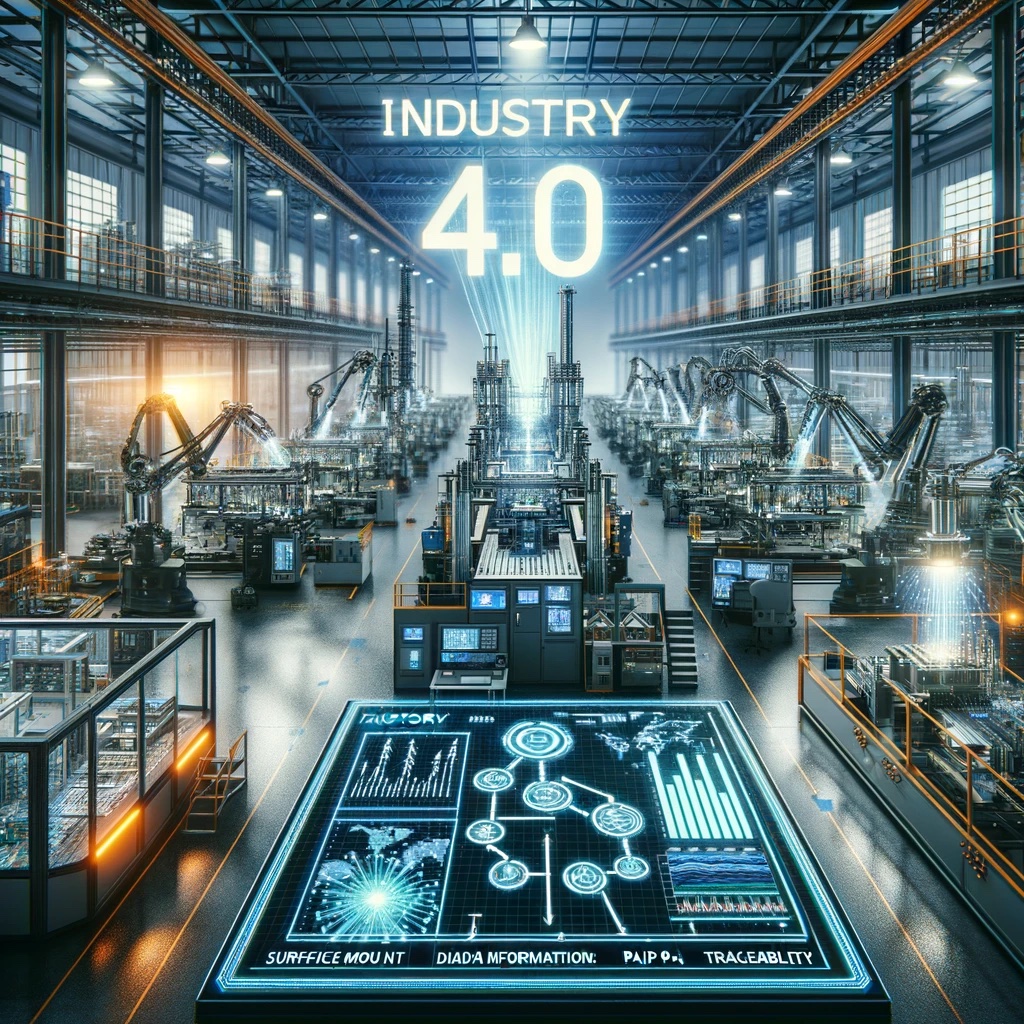
Industry 4.0/5.0 and its focus on advanced traceability represent the future of manufacturing, where efficiency, quality and customization are the standard, not the exception, enabling companies without remaining in the keeping up with market trends but also leading innovation in their respective fields.
Finally and respond to the present Draco Systems decides to apply the principles of Industry 5.0 therefore offers a qualitative leap in the integration of human collaboration and advanced automation. This evolution not only increases efficiency and productivity, but also enriches the creative process, favoring personalized and sustainable innovation. By focusing on mass customization and worker well-being, Draco can offer solutions more tailored to specific customer needs, while promoting a safer and more motivating work environment. This approach not only improves competitiveness but also strengthens sustainability and business resilience in the face of constant market changes.
quality
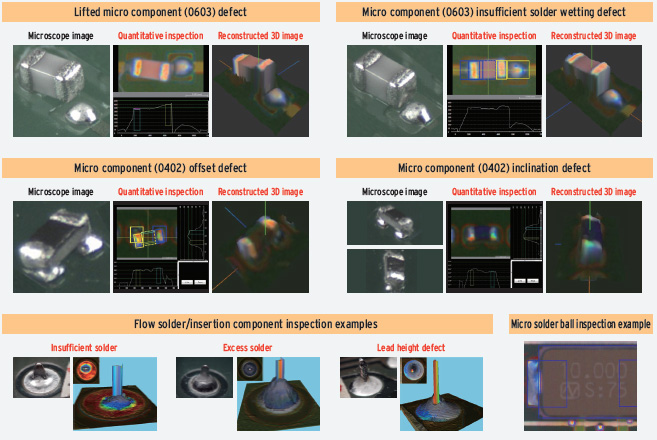
In the dynamic environment of electronic production, especially in SMD board assembly, the adoption of advanced quality processes such as 2D/3D Automated Optical Inspection (AOI), spike bed (ICT/FCT testing), functional testing, assembly and X-ray verification, form the backbone to ensure excellence in end products. 2D/3D AOI is essential for detecting surface and volume defects in components and welds, ensuring early identification of errors and compliance with quality standards. The needle bed, through the ICT (Integrated Circuit Test) and FCT (Functional Test) tests, allows to evaluate not only the correct installation of components but also the complete electronic functionality of the board, ensuring that each unit work according to specifications.
Functional testing takes this process a step further by simulating the device’s operating environment to verify its performance under real-world conditions, which is crucial for anticipating and correcting failures before they reach the end user. On the other hand, precision assembly and X-ray verification provide a detailed view of the internal layers of the boards, identifying potential hidden defects that other techniques might miss, such as cold welds or solder bridges.

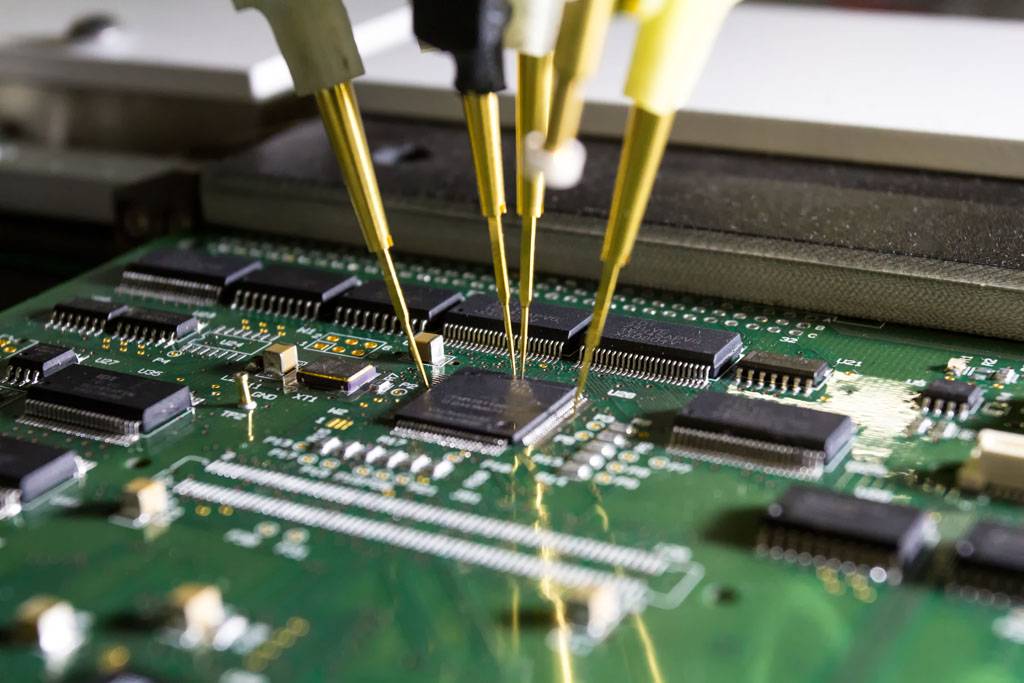
The integration of these quality processes not only raises the standard of the electronic products produced, but also reflects a commitment to excellence and innovation. This proactive approach to quality significantly reduces the risk of failure, improves customer satisfaction and strengthens the company’s competitiveness in the market. In summary, the virtues of implementing these rigorous quality controls in the production of SMD boards are critical to ensure the delivery of reliable and high-performance electronic products, positioning the company as a leader in quality and reliability in the electronics industry. .
Finish / Protections
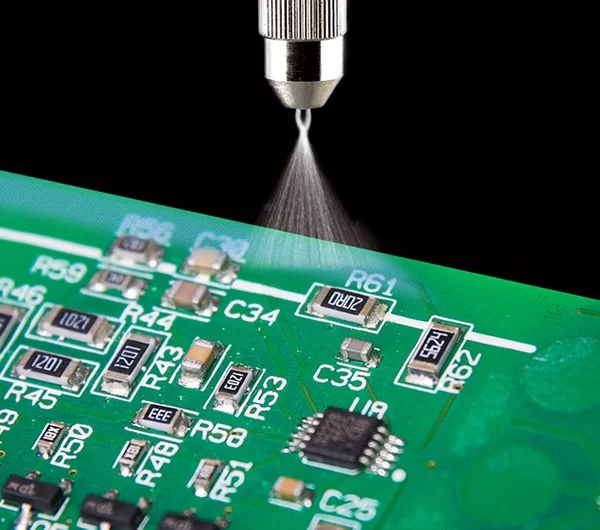

The coating of electronic boards is a crucial process that involves the application of a protective layer on the components and circuits. This practice is carried out with the aim of protecting electronic elements against adverse factors such as moisture, dust, vibrations and temperature changes, as well as possible mechanical and chemical damage. In addition, the coating helps prevent the corrosion of metals and the degradation of materials, significantly extending the useful life of the devices.
One of the main advantages of applying the coating to the boards is its ability to improve the reliability of electronic equipment. In demanding environments or in extreme conditions, this protective layer is essential to ensure the correct and continued operation of the devices. The risk of short circuits and other electrical problems is also significantly reduced, as the coating acts as an effective insulator.
In short, the coating offers robust protection and extends the life of electronic components, being an essential investment for any application that requires high durability and constant performance, especially in sectors such as automotive, medicine, or the military industry. This process not only increases the security of the devices but also contributes to the reduction of long-term maintenance and repair costs.
Potting , or encapsulated, is a procedure used in the manufacture of electronic boards to increase their protection and durability. This technique involves filling a component or an entire board with a liquid compound that, once hardened, forms a solid, protective barrier. This barrier protects the electronic components against impact, moisture, dust, vibration and other environmental factors that could damage the circuits.
One of the main advantages of encapsulation is its ability to comprehensively protect the most vulnerable components. Unlike coating , which applies a thin, superficial layer, potting completely submerges the components, offering a much more robust and complete protection. This is particularly useful in applications where the devices are exposed to extremely adverse conditions, such as in marine electronics or in devices used in heavy industrial environments.
In addition, potting also contributes to improving the dielectric strength of the assembly, thus increasing the safety of the devices in high voltage applications. This technique can help prevent short circuits and other electrical problems resulting from exposure to moisture or conductive substances.
In conclusion, encapsulation is essential for protecting and extending the useful life of electronic components under demanding conditions. With its application, manufacturers can ensure that their products are able to withstand the toughest environmental challenges, while reducing the costs associated with maintenance and repair. This makes potting a valuable investment for industries such as automotive, aerospace, defense and anyone else that requires extra protection in their electronic components.
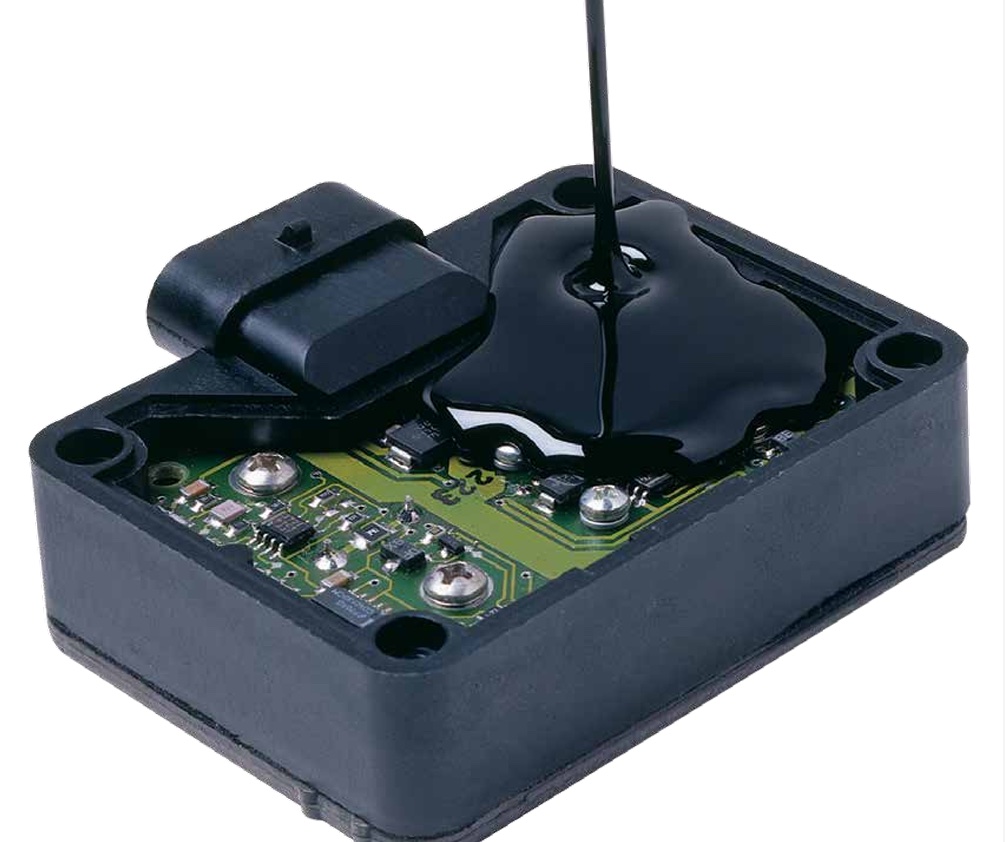
ISOs
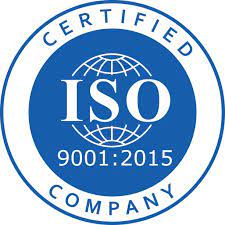
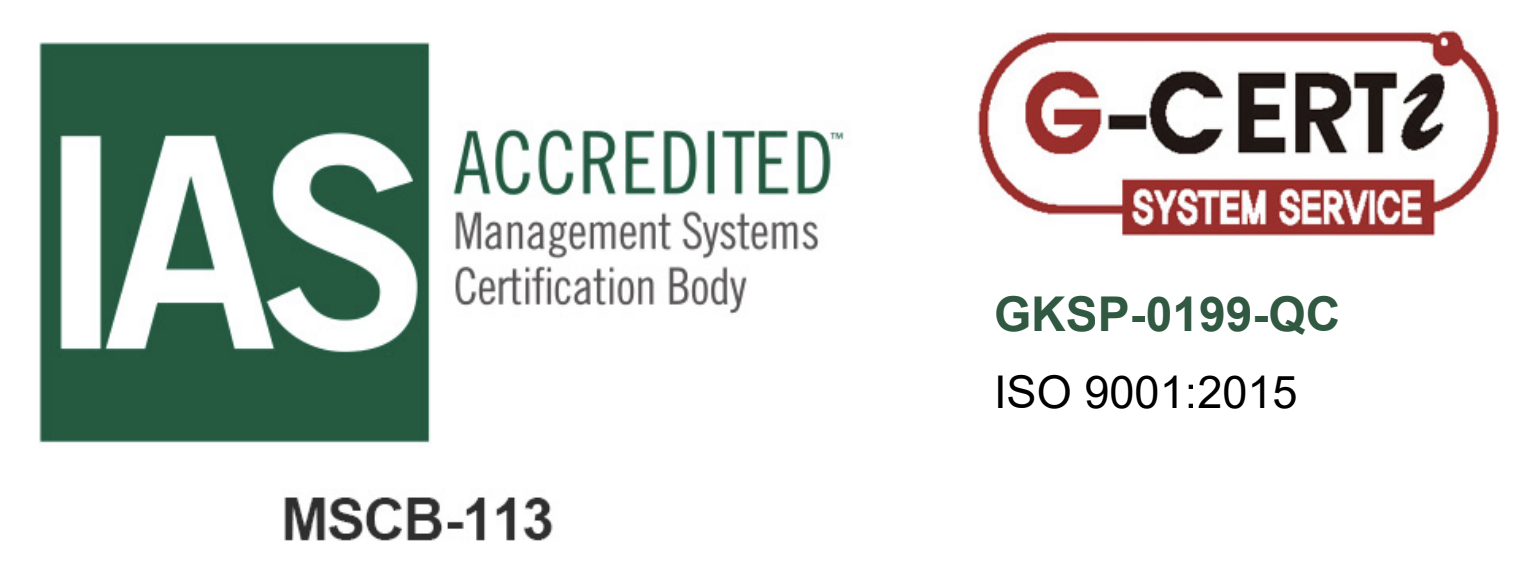
ISO 9001 is an international standard that defines the requirements for a quality management system (QMS). Having this certification is essential for companies that want to demonstrate their ability to offer products and services that meet both customer expectations and legal and regulatory requirements. Implementing an ISO 9001-compliant QMS helps improve internal processes, increase efficiency and optimize resource management, all while ensuring continuous improvement. In addition, having this certification can improve the image of the company in front of customers and can be a decisive factor in the granting of new contracts or in entering new markets. In short, ISO 9001 not only reinforces product quality and reliability, but also promotes a culture of excellence and trust between customers and suppliers. APPROVED 2024
ISO 13485 is an international standard that specifies requirements for a quality management system specifically designed for the medical device industry. This standard focuses on ensuring the conformity of medical products, patient safety and consistency in the provision of related medical services. Having ISO 13485 certification is crucial for companies wishing to operate in the global healthcare market, as it demonstrates the company’s commitment to the quality and safety of its products. It also facilitates compliance with international regulations and improves customer and other stakeholder confidence in the company’s ability to deliver products and services that are consistently reliable and secure. APPROVED 2024
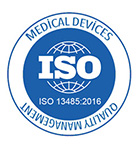
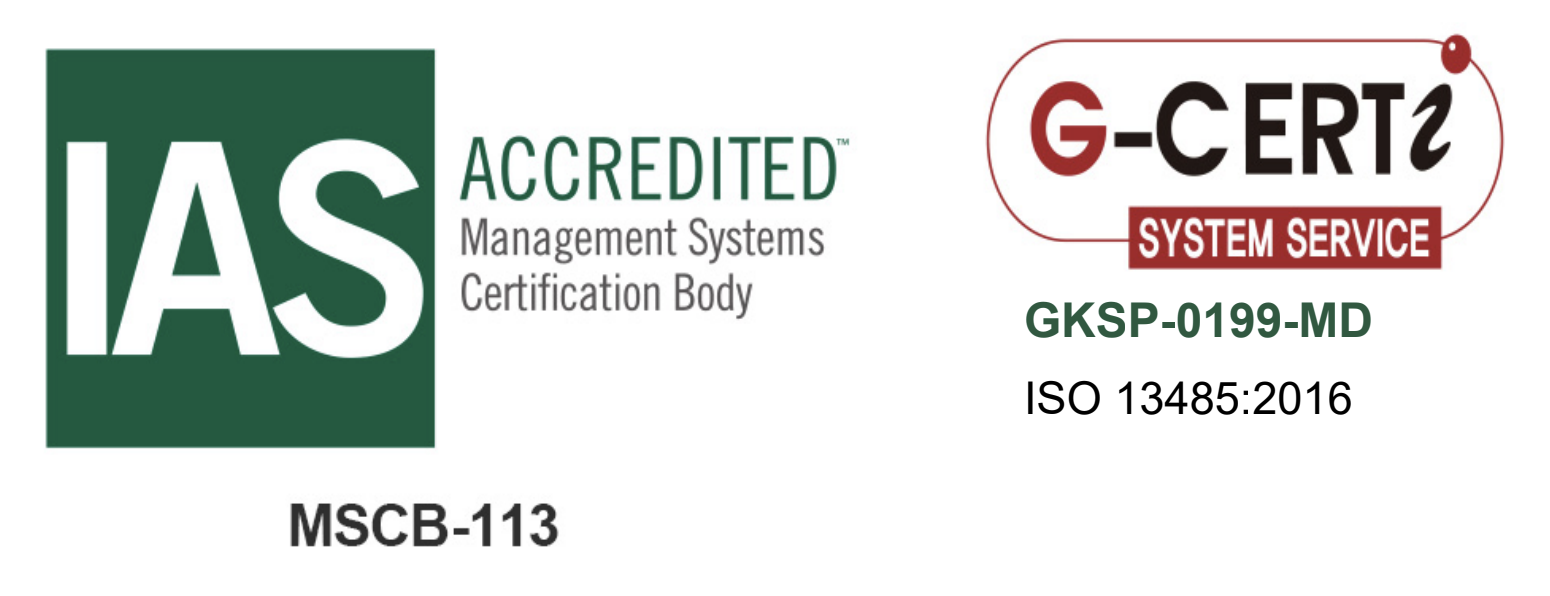
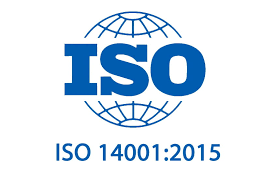
ISO 14001 is focused on environmental management systems (EMS). This standard helps organizations improve their environmental performance through more efficient management of resources and reduction of waste, thereby minimizing the environmental impact of their operations. Implementing an ISO 14001-compliant EMS not only contributes to environmental sustainability but can also offer significant economic benefits, such as cost reduction and improved corporate image. This can attract new customers who value environmental responsibility, in addition to complying with current legislation and reducing the risk of legal and reputational penalties. PROCESSING IN PROGRESS